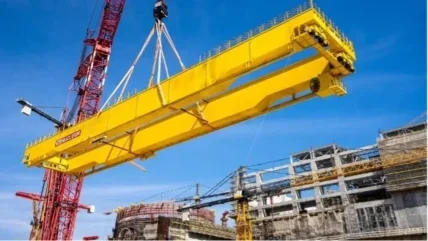
Inflation, characterised by a general increase in prices and a decrease in the purchasing value of money, poses significant challenges for various industries, including the overhead lifting equipment and material handling sector. The article explores how inflation affects the industry, examines the underlying causes, and provides strategies for companies to mitigate its impact.
Understanding inflation
Defining Inflation
Inflation is the rate at which the general level of prices for goods and services rises, leading to a decrease in purchasing power. Central banks typically aim to control inflation through monetary policy to ensure economic stability.
Causes of Inflation
Several factors can drive inflation:
- Demand-Pull Inflation: Occurs when demand for goods and services exceeds supply, leading to higher prices.
- Cost-Push Inflation: Results from increased costs of production, such as rising wages or material costs, which are passed on to consumers.
- Monetary Inflation: Caused by an increase in the money supply, leading to more money chasing the same amount of goods and services.
- Built-In Inflation: Linked to adaptive expectations, where businesses increase prices to maintain profit margins, anticipating future inflation.
Impact on the overhead lifting equipment and material handling industry
Rising costs of raw materials
Inflation often leads to increased costs for raw materials, which are crucial for manufacturing overhead lifting equipment and material handling solutions:
- Steel and Aluminium: Prices for essential materials like steel and aluminium can surge, impacting the cost of producing cranes, hoists, and other equipment.
- Electronics and Components: The cost of electronic components, critical for modern lifting equipment, can also rise, leading to higher production expenses.
Increased production costs
Higher costs of raw materials and other inputs directly impact production costs:
- Labour Costs: Inflation can drive up wages as workers demand higher pay to keep up with the rising cost of living.
- Energy Costs: Increased energy prices can significantly affect the cost of operating manufacturing plants and logistics operations.
- Transportation Costs: Higher fuel prices lead to increased transportation costs, affecting the entire supply chain.
Supply chain disruptions
Inflation can exacerbate supply chain disruptions, affecting the availability and cost of materials and components:
- Delays and Shortages: Rising costs and demand can lead to delays and shortages in the supply chain, disrupting production schedules.
- Inventory Management: Fluctuating prices make inventory management more challenging, as companies must balance the risks of holding too much or too little stock.
Pricing pressures and profit margins
Inflation can create significant pricing pressures, impacting profit margins:
- Passing Costs to Customers: Companies may need to increase prices to pass on higher production costs to customers, which can affect demand.
- Competitive Pressures: In a competitive market, raising prices can be challenging, potentially squeezing profit margins if costs cannot be fully passed on.
Capital investment and financing
Inflation can influence capital investment decisions and financing options:
- Cost of Capital: Higher interest rates, often used to control inflation, can increase the cost of borrowing, affecting investment in new equipment and technology.
- Investment Decisions: Uncertainty about future costs and economic conditions can lead companies to delay or reduce capital investments.
Strategies for mitigating the impact of inflation
Cost management and efficiency
Effective cost management and efficiency improvements can help mitigate the impact of rising costs:
- Lean Manufacturing: Implement lean manufacturing principles to reduce waste and improve operational efficiency.
- Energy Efficiency: Invest in energy-efficient technologies and practices to reduce energy consumption and costs.
- Automation and Technology: Adopt automation and advanced technologies to enhance productivity and reduce labour costs.
Supply chain optimisation
Optimising the supply chain can help manage costs and mitigate disruptions:
- Supplier Diversification: Diversify the supplier base to reduce reliance on any single source and improve supply chain resilience.
- Strategic Partnerships: Develop strategic partnerships with key suppliers to secure better pricing and ensure reliable supply.
- Inventory Strategies: Implement advanced inventory management strategies, such as just-in-time (JIT) and safety stock, to balance supply and demand.
Pricing strategies
Adopting flexible pricing strategies can help manage inflationary pressures:
- Dynamic Pricing: Implement dynamic pricing models that adjust prices based on market conditions and costs.
- Value-Based Pricing: Focus on value-based pricing to highlight the unique benefits and quality of products, justifying higher prices.
- Long-Term Contracts: Negotiate long-term contracts with customers to lock in prices and provide stability.
Financial management
Effective financial management is crucial for navigating inflationary periods:
- Hedging: Use financial instruments such as futures and options to hedge against rising material costs and currency fluctuations.
- Cost Control: Monitor expenses closely and implement cost control measures to maintain profitability.
- Capital Allocation: Prioritise capital allocation to projects and investments that offer the best return on investment (ROI) in an inflationary environment.
Case studies: industry responses to inflation
Case study 1: lean manufacturing implementation
A major crane manufacturer faced rising production costs due to inflation. By implementing lean manufacturing principles, the company streamlined its operations, reduced waste, and improved efficiency. These measures helped offset higher material and labour costs, maintaining profitability.
Case study 2: supplier diversification
A logistics firm specialising in material handling equipment experienced supply chain disruptions and rising costs. The firm diversified its supplier base, sourcing materials from multiple regions to reduce dependency on any single supplier. This strategy improved supply chain resilience and stabilised costs.
Case study 3: dynamic pricing strategy
An overhead lifting equipment company adopted a dynamic pricing strategy to manage inflationary pressures. By continuously monitoring market conditions and adjusting prices accordingly, the company was able to maintain margins and remain competitive in a volatile market.
The future of the industry in an inflationary environment
Embracing digital transformation
Digital transformation can enhance efficiency and competitiveness in an inflationary environment:
- IoT and Data Analytics: Utilise IoT devices and data analytics to monitor equipment performance, predict maintenance needs, and optimise operations.
- Artificial Intelligence: Implement AI-driven solutions to improve decision-making, forecast demand, and manage inventory more effectively.
- Blockchain Technology: Explore blockchain for transparent and secure supply chain management, reducing the risk of fraud and ensuring reliable sourcing.
Sustainable Practices
Sustainability can provide long-term cost savings and resilience:
- Renewable Energy: Invest in renewable energy sources to reduce dependence on fossil fuels and mitigate energy cost volatility.
- Sustainable Materials: Use sustainable materials and practices to reduce environmental impact and potentially lower costs.
- Circular Economy: Implement circular economy principles, such as recycling and remanufacturing, to reduce waste and create new revenue streams.
Policy and Regulation Adaptation
Staying ahead of policy and regulatory changes is crucial for long-term success:
- Regulatory Compliance: Ensure compliance with evolving regulations related to sustainability, safety, and labour practices.
- Advocacy and Engagement: Engage with industry associations and regulatory bodies to influence policy developments and advocate for favourable conditions.
- Incentive Utilisation: Leverage government incentives and programmes aimed at promoting energy efficiency, digital transformation, and sustainable practices.
Conclusion
Inflation poses significant challenges to the overhead lifting equipment and material handling industry. However, by adopting effective cost management strategies, optimising supply chains, implementing flexible pricing models, and embracing digital transformation, companies can mitigate the impacts of rising costs. Sustainable practices and proactive financial management further enhance resilience in an inflationary environment. As inflationary pressures continue to shape the economic landscape, industry players must remain agile and innovative to navigate these challenges and seize opportunities for growth.