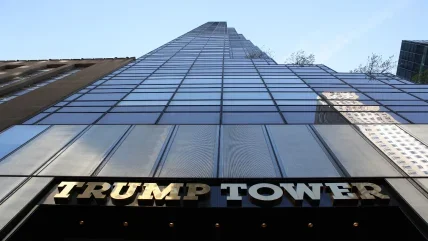
While he may have cemented his position in the consciousness of the nation by saying “You’re fired!” on the television show The Apprentice, Donald Trump has given businesses and employment rates a boost with a raft of measures that have stimulated industry in the USA—as well as creating uncertainty in certain areas due to measures such as steel tariffs. The overall result, though, appears to be steady growth.
“Business has picked up for the whole of this year,” says Mike Bunnel at OMI Crane Systems. “It’s hard not to attribute it to the new business tax situation; because corporations are paying less tax, and depreciation rules are favourable for capital expenditure, some industries are taking advantage. Growth is industry-wide, across steel, oil, concrete, and beyond.
“While the price of oil seems to have stabilised in the high 60s or low 70s—using the West Texas Intermediate—we haven’t seen a big increase in oilfield spending yet.
I think it is coming, as historically it does come after a price rise, but I don’t think any of the other crane companies have seen an increase in investment yet either. It should come later this year, and into next year.
“There has been some investment in the offshore sector, but the price of oil isn’t high enough yet to trigger major investment.”
Bret Lussow at Handling Systems International (HSI) confirms that business is good—but with a couple of caveats. “In terms of business in the US, our customers are busy, unemployment is very low,” says Lussow. “The only downside is the increase in steel prices, caused by the tariffs. Whether prices are real or artificial, it has created a price rise that has unfortunately bitten into our margins. We’re selling increased volumes of product but not necessarily seeing increased profits.
“It’s a wait-and-see game—we watch our competitors, because nobody wants to be the first to raise prices. But, our customers have been very good and understanding.”
The current level of success has revealed another issue in the sector, adds Lussow: “The main challenge for many of our customers at the moment is actually finding qualified staff. It’s hard to find young talent—we’ve recently hired four or five skilled labourers, but we could do with more. We run apprenticeships through local colleges and tech schools, and we work with the local high school to give students a first job and a first taster of work. We picked up a couple of really good young staff recently, but it’s hard to get them and it’s then hard to keep them.”
David Caputo at Capco Crane & Hoist agrees: “The economy is great, we are busy, and it seems like most companies are doing very well right now. Our region is strong and the outlook is good. The biggest problem is finding labour and good help— with the lack of trades in the North-east and the lack of young kids getting into the trades, we cannot find good help. It’s a serious threat to the growth of our industry and our business, and most companies find the same problems that they cannot find enough good help.”
And R&M Materials Handling has also seen the rise in steel prices affect business—though not enough to prevent overall gradual growth.
“The market is currently in a moderate growth cycle,” says Erin Drake, associate director for customer service and marketing at the company. “We look forward to continued moderate growth through the rest of the year. Some of this is related to overall economic growth in the Americas, as well as rising barrel prices in the oil sector.”
President at R&M Jim Vandegrift says: “R&M’s target market encompasses the Americas, with distributors in 25 countries from Canada down through Chile in South America. When considering the growth market we have been experiencing over the past 18+ months, especially within the United States and Canada, we see an unusual amount of price sensitivity in the marketplace.
“There is quite a bit of volatility in the markets we serve throughout the Americas, especially within Latin America. As for the United States and Canada, we are hopeful for a continuation of moderate growth through the end of 2018. However, trade and tariff issues between the United States and China create a level of uncertainty looking through the second half of 2018 and into 2019.”
For remote control manufacturer HBCRadiomatic, the market is doing very well across the board, boosted by the increasing focus on operator safety, says regional sales manager Ryan Stortz: “The overhead lifting market is performing very well this year. This sector is directly affected by the ebbs and flows of the economy much like most other sectors, but performance this year is very much linked to the increase in domestic manufacturing. In addition, as the market continues to embrace solutions that support advances in safety and operator efficiency, the adoption of safe radio remote control and safety-related features continues to increase.
“We have seen consistent performance across all regions. Similar to the North American market as noted above, the adoption of radio remote control in support of operator and application safety is occurring across all regions and all market segments.
As manufacturing continues to expand, there is clearly greater buoyancy in the crane/ materials handling market, and we have seen a resurgence in activity for sectors that have been depressed in recent years, such as the oil & gas and mining sectors.
“The outlook for the next few weeks, months and into next year is setting up to be very positive. Assuming the economy remains stable, and manufacturing continues on current trend, we anticipate activity in the overhead crane market to remain upbeat.”
Technology and Growth
Despite the negative impact of the steel price increases, business has been strong enough at HSI to warrant investment in a new, larger facility that will offer a range of benefits, says Lussow.
“Business is really good, and we’ve seen good growth,” he says. “Where we are, in the Rust Belt, we sell to a lot of sectors in general industry, such as heavy automotive, farm machinery, and so forth. We sell through our dealers, and they are all having a good year so far.
“Later this year we’ll be moving into a new building, with around three times more space than we currently have.
“The new premises are in McCook, around three miles away from where we are now, in La Grange, Illinois. It’s just off the interstate and it’s between the two main airports, so it’s well-connected. The new building is around 30 years old and is located in an industrial park, which offers benefits.
“We’re expanding because we can’t maintain our current level of business in our existing building—our core business is too big. There are also going to be technologies available in the new facility that will increase efficiency—for example we are installing a powder-based paint system, rather than the wet spray system that we use at the moment. The acrylic powder system uses an overhead conveyor to distribute the paint and will take up around one-fifth of the new premises. The benefits include very fast curing times of around six minutes; a reduced amount of paint used; and a harder, more abrasion-resistant finish. The current paint system has frustrated us for a number of years, despite us having played around with various recipes and processes—particularly as we’re based near Chicago so we’re regularly affected by the weather. Sometimes it can take two or three days after painting before we can ship the cranes. So the faster cure times will improve efficiency dramatically.
“We will also have better unloading and loading docks, which will increase efficiencies too, and increased storage space means we can bulk-buy steel at a better price.
We’ll also be able to store it indoors, which reduces preparation time when welding and painting—and we can buy blue steel, again reducing preparation time.
“Overall we are very pleased—we’ve experienced some growing pains but we’ve weathered the storm, and we’re excited about the new facility.”
Bunnel at OMI Crane Systems says the company is working with the current trend towards automation—and improving its efficiencies: “We are starting to see a push in steel service centres for automation, so we are working towards the technologies that can facilitate that, such as position sensing and data gathering. If you eliminate the human element you increase efficiency, and you get more out of existing facilities.
And, you get no mistakes. We currently have a partnership with an automation specialist and we are working together to refine that technology.
“In terms of other changes, we are now more vertically aligned than before, simply because of an inability to find reliable suppliers. We’ve made space to produce many of our own components—when you’re running at higher capacities, you need to be able to control your own destiny.”
R&M Materials Handling has introduced a range of products to cover a wide variety of end use applications—and the company is also focusing on developing its digital interface to assist its distributors, says Drake: “Our LK electric chain hoist is still fairly new to the market, and we continue to make improvements to the product and delivery. Our goal with this product is to reduce downtime and maintenance costs. The hoist is very robust, and the parts and components are designed to be easily accessed for maintenance checks and service.
“We recently developed additional models for our flexible trolley gauge solution for double girder hoists. This is a special load beam design that allows us to cover a wide range of existing gauges—the perfect solution for a replacement double girder hoist.
“We have also recently released our DXW wire rope hoist. This is a heavyduty double girder hoist with capacities up to 160 tons. It is designed for Class D operations, and is available as part of a modular crane package.
“R&M has the broadest product portfolio in the industry, so our products are being used in a wide range of applications and industrial sectors, from metal fabrication to textile production to mining and oil and gas applications.
“In addition to our product developments, we have made many improvements to our digital tools and e-commerce platform. We want our distributors to have an easy time working with us, and this has been one of the key drivers to helping them to do their jobs as quickly and effectively as possible.”
The current strength of the industry in the USA has given Capco’s business a boost across numerous sectors, says Caputo: “We have been doing plenty of crane systems, from new cranes and runway steel, stainless steel systems for food grade applications and plenty of mod work and retro work; cutting down cranes, redoing the controls and adding new radio and PLC systems.
Work is coming from all over and varies in scope and size—the economy is great. We’re supplying the power industry, plastics, wind power and steel fabricators, to mention some of the work in house.”
HBC-radiomatic is expanding the capabilities of its product range, to serve the wide range of sectors the company serves, says Stortz: “The applications for radio remote controls are virtually limitless. HBC-radiomatic has a very broad portfolio of products that can be applied to any type of application. HBCradiomatic controls are used in many different industries including mining, manufacturing, oil and gas, entertainment, utilities, construction, agriculture, transportation, automation and logistics.
“HBC-radiomatic will continue to invest in the development and the definition of the state of the art for radio control technology and functionality, and we anticipate the use of safe radio remote control to keep expanding as new features solve problems that cannot be adequately addressed with tethered control options.
“As the global leader in radio remote controls, HBC-radiomatic is continually developing new products to meet the changing demands of the marketplace. HBC has recently released a complete package system, micron M, for the overhead crane market. HBC has updated the technology in our plug-and play 300 series receivers which include integrated light and horn. HBC has also expanded the display capabilities and functionality in our most powerful handheld transmitter, micron 7, as well as in the best-selling spectrum series of bellybox style transmitters.
“Updates to HBC’s most ergonomic belly-box style transmitters, the technos series, includes TFT displays, integrated flashlights, and front panel lighting. Other new developments include safety features such as radiomatic photon which will provide live video feedback, enabling switches with touch activation, as well as new Li-ion batteries with an on-board power meter that provides operators with more accurate information regarding the amount of remaining battery life.
“The capability of today’s radio remote controls can offer the same amount of control as if the operator were in the cabin, at the control station, or using a pendant.
The operator can now have extensive machine feedback from the equipment via a display screen, LEDs, audible or haptic feedback and even live video feedback. The biggest advantage of having all of this in the operator’s hands is that it allows them to physically position themselves in the safest area with the best possible vantage point for the work being performed. Also, this allows the operator to inspect the rigging and improve communication on the jobsite or on the factory floor.”